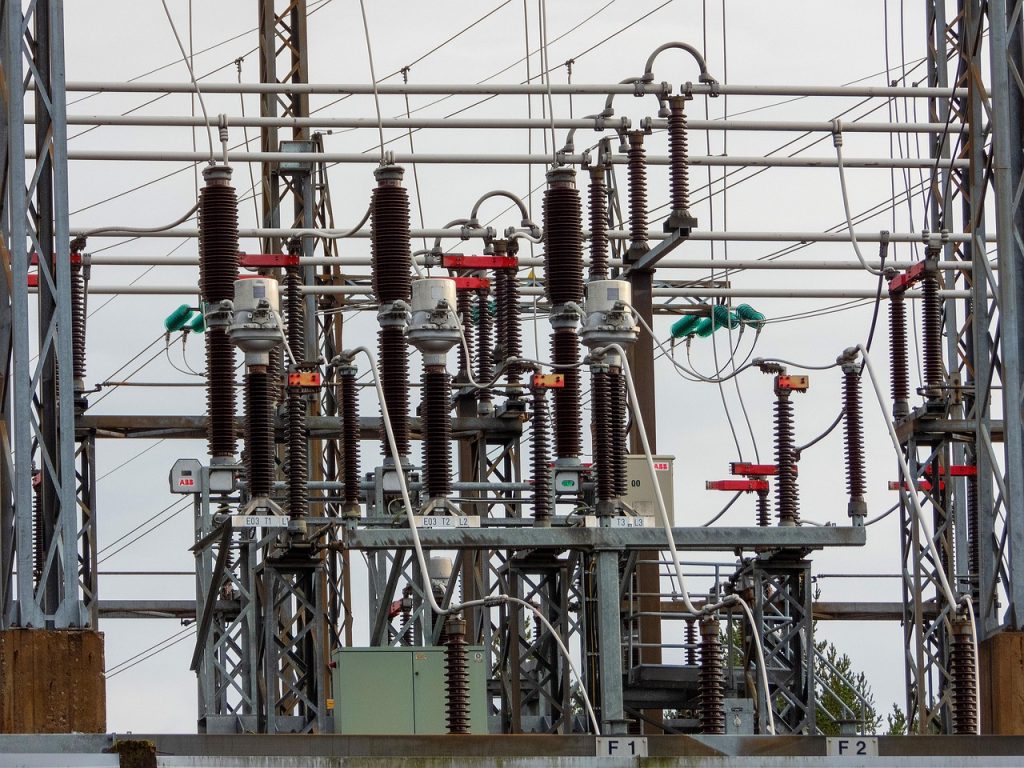
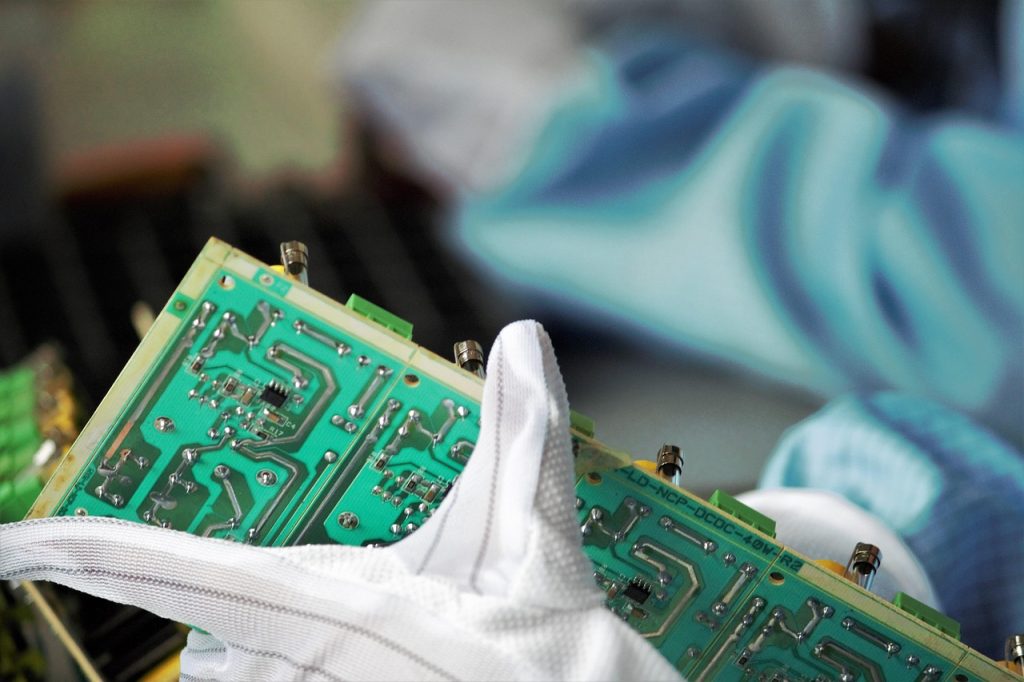
Technical characteristics and production process differences
The manufacturing process of film capacitors mainly includes film stretching, metallization, winding/lamination and packaging. The key technology lies in the uniformity control of dielectric film and the fine patterning of metallized electrodes. Advanced evaporation technology can achieve electrodes with nanometer-level thickness control, while slitting technology determines the final dimensional accuracy of the capacitor. In terms of materials, polypropylene (PP) film has become the first choice for high-frequency applications due to its low loss and high voltage resistance, while polyester (PET) film has more advantages in cost-sensitive applications.
The production process of electrolytic capacitors revolves around special processes such as anode etching, formation, and electrolyte injection. The etching technology of the anode foil determines the surface area expansion multiple, which directly affects the final capacity; the formation process accurately controls the thickness and quality of the oxide film. The liquid electrolyte formula is a core technical secret, involving a complex balance of solvents, solutes and additives. Solid electrolytic capacitors use conductive polymers instead of traditional electrolytes, which significantly improves high-frequency performance and reliability.
In terms of technological innovation, film capacitors are developing towards ultra-thinness (<1μm) and high temperature (above 150°C), and the metal edge thickening technology improves the self-healing performance. Electrolytic capacitors are committed to low ESR, long life and solid state, and new conductive polymer systems continue to break through performance limits. Both types of capacitors face the challenge of lead-free and halogen-free material innovation under environmental protection requirements.