Summary
DC link capacitors are key components in power electronic systems, and their quality directly affects the stability and reliability of the entire system. This article will systematically explain the methods and strategies to ensure the excellent quality of DC link capacitors from four key aspects: design, production process, quality control, and finished product testing. By analyzing the control points of core parameters such as ESL and ESR of DC link capacitors, a complete quality management system is provided to ensure that DC link capacitors can maintain excellent performance and uniformity under harsh working environments such as high temperature, high humidity, and high ripple current, meeting the needs of industrial applications for high-reliability DC link capacitors.
- Design is the basis for ensuring the quality of DC linkcapacitors
DC link capacitors need to fully consider various key parameters and performance indicators in the design stage, which is the basis for ensuring the quality of the final product. When designing DC link capacitors, it is necessary to focus on three aspects: dielectric material selection, structural layout optimization, and electrical parameter calculation. The material and thickness of the dielectric film directly affect the withstand voltage level and capacity stability of the DC link capacitor. Polypropylene (PPS) or polyester (PET) film is usually selected to obtain excellent dielectric properties and temperature characteristics. The ESL of the DC link capacitor must be controlled at an extremely low level (usually <50nH), which needs to be achieved by optimizing the internal electrode structure and terminal design. At the same time, the ESR of the DC link capacitor also needs to be accurately calculated, which is related to the temperature rise characteristics and power dissipation capacity of the capacitor at high frequencies. The heat dissipation path and mechanical fixing method of the DC link capacitor should also be considered during design to ensure that it can maintain a stable connection under vibration. Computer-aided simulation can be used to pre-evaluate the electric field distribution and thermal field distribution of the DC link capacitor to avoid partial discharge and hot spots. An excellent DC link capacitor design should be able to maintain a capacity change rate of less than ±5% and a loss tangent value (tanδ) of less than 0.003 within a working temperature range of -40℃ to +105℃.
- The production processdetermines the core performance of the DC linkcapacitor
The DC link capacitor needs to be strictly controlled at every sector during manufacturing process, and any slight deviation may lead to a failure in the performance of the finished product. The primary key to manufacturing DC link capacitors is to maintain the cleanliness and temperature and humidity stability of the production environment. The coating process of the metallized film must ensure thickness uniformity and accurate edge margin. The ESL of the DC link capacitor depends largely on the accuracy of the winding process. The tension control and alignment accuracy of the automatic winding machine must be kept within ±0.1mm. In the welding process, the ESR of the DC link capacitor is directly related to the quality of metal spraying, and the spraying parameters need to be optimized to obtain low-resistance connections. The vacuum impregnation process of the DC link capacitor is crucial to the long-term reliability of the product. It is necessary to ensure that the impregnant is fully penetrated and all bubbles are excluded. The process test is a key step to improve the stability of the DC link capacitor. Potential defective products can be screened out through process test. Statistics show that the failure rate of DC link capacitors with strict process control can be reduced by more than 60%.
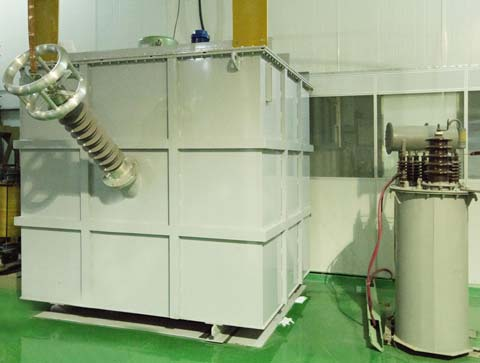
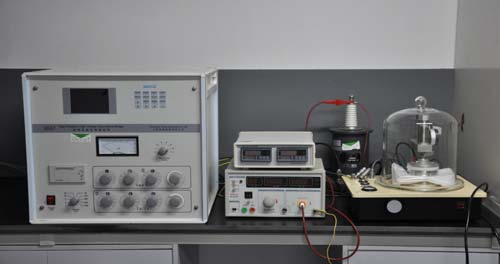
- Quality control is the guarantee of the reliability of DC linkcapacitors
Establishing a comprehensive quality control system is also the key to ensuring the stable quality of DC link capacitors. For DC link capacitors, quality control should be carried out throughout the entire production process from the entry of raw materials into the warehouse. Each batch of metallized film must be tested for parameters such as square resistance, withstand voltage and tensile strength before being put into use. These basic material properties directly affect the ESR and life of the DC link capacitor. The online detection system should monitor the winding density, diameter deviation and appearance defects of the DC link capacitor in real time, and any element that exceed the tolerance should be removed in time. The ESL test of the DC link capacitor requires a high-frequency impedance analyzer to ensure that its value meets the design specifications. The destructive tests conducted by sampling include life aging test and mechanical strength test, which can verify the internal structural integrity of the DC link capacitor. The quality control department should also establish a batch traceability system for DC link capacitors to record the process parameters and test data of each batch of products for subsequent quality analysis. Practice has shown that the failure rate of DC link capacitor manufacturers that implement strict quality control can be controlled below 0.001% on the client side
- Finished product testing is the last line of defense before DC linkcapacitors leave the factory
Comprehensive finished product testing is the last checkpoint to ensure the excellent quality of DC link capacitors. Each DC link capacitor must undergo rigorous electrical performance testing before leaving the factory, including basic parameters such as capacity, loss tanδ, insulation resistance and withstand voltage. LCR meter testing is particularly critical for evaluating the ESL of DC link capacitors. The ESR of DC link capacitors needs to be accurately measured by LCR meter.High-temperature load testing can simulate the performance of DC link capacitors in actual working environments, and requires continuous testing for more than 1,000 hours at rated voltage and maximum operating temperature by sampling. For the mechanical reliability of DC link capacitors, vibration testing and terminal strength testing are also required to ensure that they can still work stably in harsh environments. Advanced testing systems can automatically record the test data of each DC link capacitor and generate quality reports, which are of great reference value for subsequent quality improvements. Statistics show that the failure rate of DC link capacitors that have been fully tested and screened can be reduced hugely. It is particularly important to emphasize that the test conditions of DC link capacitors must strictly comply with relevant international standards
- Continuous improvement is a long-term mechanism to improve the quality of DC link capacitors
Establishing a continuous improvement mechanism is the key to ensuring the continuous improvement of the quality of DC link capacitors. Manufacturers of DC link capacitors should systematically collect product working condition data and failure cases at the client end, and analyze the common failure modes and root causes of DC link capacitors. For the problem of high ESL of DC link capacitors, improvements can be achieved by optimizing the internal structure and connection method. The stability of the ESR of DC link capacitors also requires long-term research from material technology. Regularly review the design specifications, process standards and quality control plan of DC link capacitors, and update them in a timely according to new technology development and market demand. Establish a reliability database for DC link capacitors to provide data reference for the products improvement. Practice has shown that DC link capacitor manufacturers that implement continuous improvement plans can improve product performance effectly. It is particularly noteworthy that the improvement of DC link capacitors should follow the closed-loop process of “design-verification-implementation” to ensure that each change is fully verified.
- The impact of supply chain management on the quality of DC linkcapacitors cannot be ignored
A high-quality supply chain is an important basis for ensuring the stability of the quality of DC link capacitors. The core materials of DC link capacitors, such as films, impregnant and packaging materials, must be selected from certified high-quality suppliers. Establish a strategic partnership with suppliers to ensure the quality consistency and long-term stable supply of key materials Pay special attention to the purity of conductive materials that affect the ESL of DC link capacitors, and the performance of soldering materials that affect the ESR of DC link capacitors. Implementing suppliers performance evaluation system and regularly review the quality management system of raw materials suppliers for DC link capacitors. In film capacitor industry,Data shows that optimizing supply chain management can increase the uniformity of DC link capacitors by more than 20%. It is particularly important to emphasize that material changes in DC link capacitors must undergo a rigorous evaluation and verification process to ensure that there will be no negative impact on product reliability.
Conclusion
To ensure the excellent quality of DC link capacitors, a comprehensive quality management system needs to be built from multiple aspects such as design, process, testing and supply chain. As key performance parameters, the ESL and ESR of DC link capacitors must be strictly controlled at all stages. By optimizing the structural design of DC link capacitors, precisely controlling the manufacturing process, implementing strict quality inspections and establishing a reliable supply chain, it can be ensured that DC link capacitors can exhibit excellent reliability and stability under various harsh working conditions. In the future, as power electronics technology develops towards high frequency and high power density, the performance requirements for DC link capacitors will continue to increase, and manufacturers need to continue to innovate and improve to meet the market demand for high-quality DC link capacitors. by enhancing quality awareness in every sector of DC link capacitors production that excellent DC link capacitor products can be truly produced.